Cest / Decest

FMT is able to study and create complete sterilisation systems for full containers, whether they are cans, glass or plastic containers.
In relation to the project, considering the production speed, the type of product and layout needs, FMT is able to offer both robotic and traditional basket loading and unloading systems.
The FMT traditional basket loaders and unloaders are very sturdy machines, designed to work in wet environments and move heavy loads.
These machines carry out the entire loading and unloading phases of containers into the baskets. They are available in automatic and semi-automatic versions.
The machines can be combined with the shuttle to carry out the handling operations and the unloading/loading of the baskets from/to the retorts.
An essential feature of the FMT machine is the ability to be customised in the main functions, in relation to Customers requirements.
Customisations can concern components such as:
- Type of container pick-up head
- Machine layout
- Work height
- Basket dimension
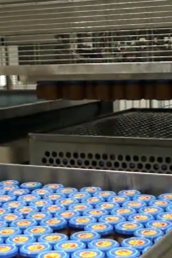
Depalletisers
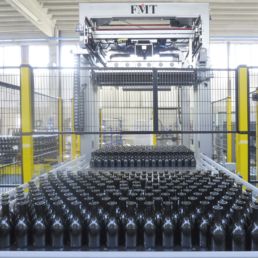
FMT has developed its range of automatic depalletisers with particular attention to flexibility, in order to be able to process different types of containers with the same machine.
Thanks to the development by “blocks”, each Customer can personalize the machine in relation to the degree of required automation.
In fact, the FMT Depalletisers can be composed starting from a semi-automatic machine up to a “full optional” model, with a maximum degree of automation and autonomy even at high line speeds (up to 1.000 cpm)
Special attention to the choice of high quality materials and a sturdy structure are the key elements of this FMT product range, that make it possible for us to ensure high performance levels over the years.
The different Depalletiser models can be equipped with:
- Automatic system for the withdrawal of layer pads
- Automatic pallet feeding and unloading system
- Buffer belt conveyor and alignment system, on a single row, for containers outfeed
- Low level - GEMINI Model.
- High level - ATHENA Model
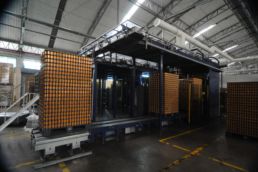
Traditional Palletisers

FMT has developed its range of automatic palletisers for processing cartons, shrink-wrapped packs and trays.
The product can be fed from above or below
The palletiser can also be of the Multiliner type, capable of processing simultaneously two or more types of differently sized packages and capable of palletising them separately
Special attention to the choice of high quality materials and a sturdy structure are the key elements of this FMT product range that make it possible for us to ensure high performance levels over the years.
The different palletiser models can be equipped with:
- Automatic layer pad deposit system
- Pallet destacker storage unit
- Integration with automatic pallet winder
The palletisers can have two configurations
Storage Systems / Conveyors
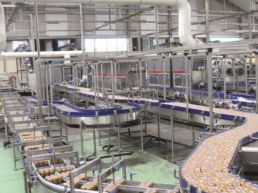
As a supplier of complete lines, over the years FMT has developed several containers handling systems to meet the needs of its Customers.
In fact, in order to have lines with high production efficiency, it is essential to have conveyors and storage systems with high quality and advanced technology.
Behind each line, there is a very important engineering design that uses all available handling technologies to be able to develop the best final solution for each project.
Among the various FMT systems to complete its lines, we have:
- Belt conveyors
- Elevators / lowering devices for cartons or single containers
- Drying tunnel
- Empty or full containers washing machines
- Buffer (FIFO or LIFO)
- Containers overturning machines
- Tilting conveyors for cap sterilisation (Hot Fill)
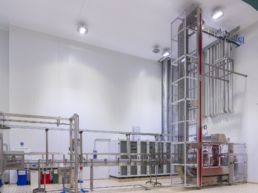
Basket Load / Unload Robot
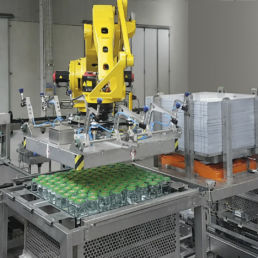
Robotic basket loading and unloading system for new and existing sterilisation retorts.
The system is designed and studied to receive containers from the filling line, place them inside the basket which will then be directed towards the sterilisation retorts.
After sterilisation, the baskets return to the Robot, which will unload the containers and send them to the packaging line.
The system is tailor-made and gives the possibility of making maximum use of space available.
The possible coupling with suction cup pick-up systems and arms on the heads enables the combined pick-up of the interlayers.
The Robotic basket loading and unloading technology was developed for both medium and high speeds.
SPEED from 2 to 4 layers per minute
The basket loading and unloading system with Robot has different customisation options. Its main feature is flexibility, as it is a technology that can be configured based on specific Customer’s requests:
- Possibility to manage both the basket loading and unloading functions with a single Robot.
- Flexibility, reliability and full traceability of the containers
- Thanks to different types of special multifunction heads, the robotic system is able to meet the packaging needs of most containers.
- Thanks also to the various types of baskets, to be chosen according to the type of container, the system becomes universal, suitable for any type of container, such as: metal cans, glass jars, pouches, plastic cups
- Very fast format change
- Expandable for increased production
- High residual value of the robot over time
- Reduced maintenance costs
- Pick-up head with suction cups
- Magnetic pick-up head
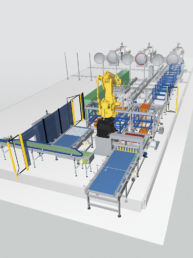
Pick and Place
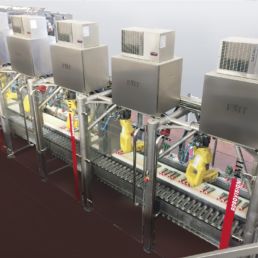
Packaging system with Pick & Place Robot.
The system is designed and developed to receive containers from the filling line, to place them inside the package, or on a conveyor belt, which will then be directed towards the additional packaging area or palletising area.
The system is tailor-made and gives the possibility of making maximum use of space available.
By using the modularity of all the platform elements and combining the robot with the pick-up heads, it is possible to find the solution that best suits the different requirements in the world of packaging.
- Flexibility, as this technology can be configured according to specific Customer’s requirements
- Precise positionig of the container in the pack
- Tailor-made design making maximum use of space available
- Reduced installation costs, the equipment is supplied assembled and wired, positioned on a skid
- High residual value of the robot over time
- Reduced maintenance costs
- Product packed in one or more layers
- Possibility of different levels of automation
- Expandable for increased production
- Thanks to different types of special heads, the robotic system is able to meet the packaging requirements of most containers
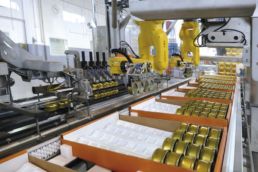
Robot Palletisers
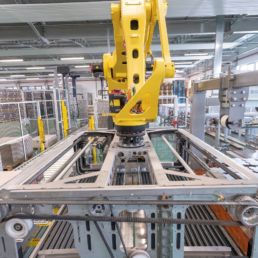
The ZEUS Robotic palletising systems are developed to meet the most modern needs of the food industry. Thanks to a wide variety of special multifunction heads, they are able to meet the packaging needs of most containers and packages.
In particular, they represent an alternative to traditional palletising systems.
The possible coupling with suction cup pick-up systems and arms on the heads enables the combined pick-up of empty layer pads and pallets.
The ZEUS Robotic palletising has been developed for both low speed and high speed.
SPEED from 3 to 120 ppm
(*) The speed depends on the size of the package and the palletising layout.
The Palletising system with Robot has different customisation options. Its main feature is flexibility, as it is a technology that can be configured based on the specific customer requests:
- Possibility of palletising several lines simultaneously
- Ability to palletise packages of different size and type simultaneously
- In most cases, format change without the need for mechanical intervention. Carried out by program insertion or selection
- Limited installation space
- Expandable for increased production
- Reliability, flexibility and possibility to reconvert the system
- High residual value of the robot over time
- Pick-up head with suction cups
- Pick-up head with pneumatic or motorised grippers
- Pick-up head with rack
- Magnetic pick-up head
- Basket pick-up head
- etc....
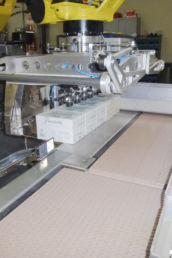
Palletizer configurations:
Sterilization Retorts
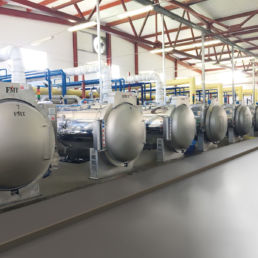
“FLEXI” STERILISATION RETORT
It is a modular range of Retorts for the sterilisation and pasteurisation of foodstuffs inside any type of container: metal cans, glass jars, pouches, plastic trays, tetra paks.
An extremely flexible and innovative work platform, designed to meet the sterilisation needs of the most demanding Customers.
Advanced technological solutions that enable FMT to create complete sterilisation machines and systems, at the highest levels, available on the market today.
- Fast, high-quality thermal treatment
- Easy operation and maintenance
- Maximum care for delicate products
- Same Retort, DIFFERENT STERILISATION CYCLES
- Modular configuration
- Energy saving systems
- Laboratory Retort
- Static Retort
- Rotary Retort
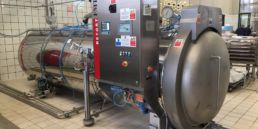
Filler with flow meters
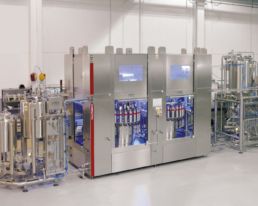
The electronic filler with Flow meters is ideal for filling viscous, dense or liquid products that require a high level of hygiene, such as, for example, milk-based products such as Drinkable yoghurt or Oil, Vinegar, Syrups or Toppings.
Thanks to the use of flow meters, the machine is completely electronic and can be subjected to a fully automatic CIP cycle to ensure sanitising of the entire circuit. Filling takes place without contact between the valve and the container, minimising the possibility of contamination.
The filling phases can be set via the machine PLC, making it easy to use and ensuring recipe repeatability.
The FMT electronic fillers with Flow meters can have two types of flow meters, defined according to product conductivity:
- Magnetic: for products with standard conductivity
- Mass: for products with conductivity below 20μS/cm
- Automatic dummy bottles system
- Customised nozzles in relation to the product
- Possibility of “counter-current” washing
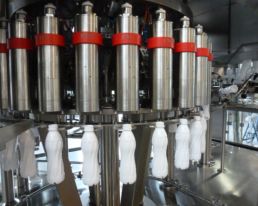
The various technologies of the filler with flow meters can be found in two configurations:
Piston fillers
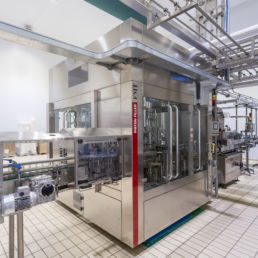
This technology is ideal for filling any type of viscous or dense product, with or without pieces such as, for example, marmalades, sauces, ketchup, mayonnaise, pât, baby food, honey, spreads.
Using a mechanical technology for the filling, the Piston filler also has the advantage of being very robust and easy to use equipment for operators.
It is extremely flexible and can be adapted to the filling of different types of products
- Standard valve or “rotary” valve.
- Valve with Horizontal or vertical plungers.
- Valve with membrane.
It is available both in the linear version, for low speeds, and in the rotary version for medium-high speeds.
- Filling from the bottom
- Automatic piston extraction system for CIP
- Customised nozzles in relation to the product
- Conical or cylindrical valves or with membrane
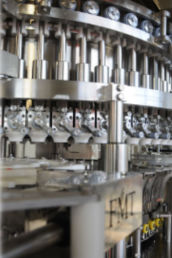
The various technologies of the piston filler can be found in four machine versions: